摘要:在70t軋機(jī)上,以1100 ℃為開軋溫度,采用2~4道次大變形軋制方式制備超細(xì)晶TC4鈦合金,研究了變形量(60%~90%)對(duì)該合金組織和性能的影響.結(jié)果表明:TC4鈦合金中的α和β相片層狀組織在熱軋過程中因動(dòng)態(tài)再結(jié)晶被分解成超細(xì)晶組織,由于動(dòng)態(tài)再結(jié)晶不完全,組織中存在殘留位錯(cuò);隨著變形量增加,超細(xì)晶的數(shù)量增加且晶粒尺寸減小,合金強(qiáng)度增大,且塑性保持良好,拉伸斷裂方式均為韌性斷裂:經(jīng)變形量為90%的大變形熱軋后,得到了高強(qiáng)高韌超細(xì)晶TC4 鈦合金,其平均晶粒尺寸約 150nm,抗拉強(qiáng)度達(dá)1135 MPa,伸長(zhǎng)率超過9%。
引 言
TC4(Ti6Al4V)鈦合金是一種典型的雙相(α+β)鈦合金,具有密度低、強(qiáng)度高、熱膨脹系數(shù)低、生物相容性好、抗疲勞和耐腐蝕性能優(yōu)異等特點(diǎn),被廣泛用于航空航天、汽車、海洋工程、化學(xué)工程、醫(yī)療器械等行業(yè)[1G2].然而,使用條件的變化對(duì)合金的強(qiáng)度提出了更高的要求,如何進(jìn)一步提高 TC4鈦合金的強(qiáng)度成為近十年來鈦合金研究的熱點(diǎn)之一.晶粒(組織)細(xì)化是同時(shí)提高材料強(qiáng)度和韌性的有效途徑,采用強(qiáng)烈塑性變形(SeverePlasticDeformation,SPD)技術(shù)可以獲得納米晶(晶粒尺寸在100nm 及以下)或超細(xì)晶(晶粒尺寸在1000nm 及以下)組織,進(jìn)而顯著提高材料的強(qiáng)度.近年來,各種 SPD 技術(shù),如高壓扭轉(zhuǎn)(HPT)[3]、等通道擠壓(ECAE/ECAP)[4]等,被廣泛應(yīng)用于制備高強(qiáng)度 TC4鈦合金,并取得了良好的效果[3G9].但是,這些傳 統(tǒng) SPD技術(shù)對(duì)生產(chǎn)條件的要求較高,制備的材料尺寸也較小,很難實(shí)現(xiàn)工業(yè)化生產(chǎn).軋制是最常用也是最理想的工業(yè)化生產(chǎn)大型板材的方法,作為一種新型的 SPD 技術(shù),大變形軋制能有效地細(xì)化晶粒,同時(shí)易于實(shí)現(xiàn)工業(yè)化生產(chǎn).在前期研究 中,作者所在課題組采用大變形軋制方法成功制備了納米晶 及超細(xì)晶鋼[10G12]、鎳合金[13]和純鈦[14G15].在此基礎(chǔ)上,作者采用道次大壓下量的大變形熱軋方法制備超細(xì)晶TC4鈦合金,研究了軋制變形量對(duì)該合金組織和性能的影響。
1 試樣制備與試驗(yàn)方法
試驗(yàn)原料為商用 TC4 鈦 合 金,由云南鈦業(yè)供,其化學(xué)成分見表1.使用電火花線切割機(jī)在 TC4鈦合金上切割出尺寸為100mm×30mm×20mm 的塊狀試樣,在馬弗爐中于1100 ℃保溫1h,然后在70t軋機(jī)(上海應(yīng)用技術(shù)大學(xué)金屬壓力加工中心)上進(jìn)行道次大壓下量軋制,開軋溫度1100 ℃,經(jīng)2~4道次軋制至厚度分別為8,6,4,2mm,軋制變形量分別為60%,70%,80%,90%,終軋溫度600 ℃,水冷至室溫。
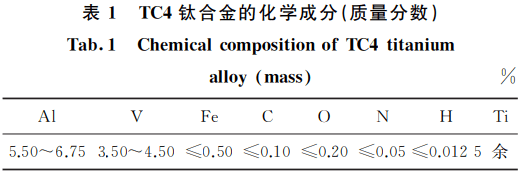
在大變形熱軋前后的 TC4鈦合金上取樣,經(jīng)鑲嵌、研磨、拋光后,用 Kroll腐蝕溶液(由3mL HF、6mL HNO3 和100mL H2O 組成)腐蝕10s,再在ZEISSAXIOImager.A1m 型光學(xué)顯微鏡上觀察顯微組織.用 MTPG1A 型電解雙噴減薄儀制備薄膜試樣,雙噴液為體積分?jǐn)?shù)5%高氯酸酒精溶液,溫度控制在-30 ℃左右,電壓為30V,然后采用JEOL2100F型高分辨透射電子顯微鏡(TEM)進(jìn)行形貌觀察和結(jié)構(gòu)分析,工作電壓為200kV,通過對(duì)10張暗場(chǎng)像的晶粒尺寸(晶粒數(shù)大于100個(gè))進(jìn)行統(tǒng)計(jì),計(jì)算平均晶粒尺寸.對(duì)大變形熱軋前后的 TC4鈦合金試樣進(jìn)行研磨、拋光,再用體積分?jǐn)?shù)5%高氯酸酒精溶液電解拋光 并 去 應(yīng) 力 處 理 后,用 ShimadzuXRDG6000型 X射線衍射儀(XRD)進(jìn)行物相分析,
采用銅靶,Kα 射線,電壓40V,電流40mA,掃描范圍為30°~90°.使用402SXV 型顯微硬度計(jì)進(jìn)行維氏硬度測(cè)試,載荷為4.903N,保載時(shí)間為15s.根據(jù) ASTM E8/E8M 設(shè)計(jì)拉伸試樣,尺寸如圖 1 所示,RD,TD,ND 分別為軋制方向、橫向和法向;根據(jù) GB/T228-2002,在 Zwick/RoellGZ100型萬能拉伸試驗(yàn)機(jī)上進(jìn)行室溫拉伸試驗(yàn),拉伸應(yīng)變速率為1×10-3s-1.
2 試驗(yàn)結(jié)果與討論
2.1 顯微組織
由圖2可知:大變形熱軋前 TC4鈦合金的組織由片層狀α和β雙相組成,原始等軸狀晶界清晰,平均晶粒尺寸約400μm;隨著變形量的增加,其組織顯著細(xì)化;在60%和70%變形量下 TC4鈦合金的原始粗大晶粒被壓扁拉長(zhǎng),且在變形過程中由于位錯(cuò)增殖,粗大晶粒內(nèi)部被分割成細(xì)小的亞晶粒;當(dāng)變形量為80%時(shí),合金中晶粒的完整形貌消失,出現(xiàn)明顯的軋制變形帶;當(dāng)變形量為90%時(shí),合金中的變形帶更加細(xì)密和均勻,組織更加細(xì)小.由圖3可見:大變形熱軋后TC4鈦合金發(fā)了強(qiáng)烈塑性變形,組織明顯細(xì)化,變形量為 60%時(shí),鈦合金組織中存在超細(xì)晶和一定程度的位錯(cuò);隨著熱軋變形量的增加,超細(xì)晶數(shù)量增加,晶粒尺寸略有減小,位錯(cuò)密度變化不大;當(dāng)熱軋變形量為80%時(shí),TC4鈦合金中的超細(xì)晶數(shù)量較多、晶界相對(duì)清晰,當(dāng) 變形量超過 90% 后,超細(xì)晶晶界不清晰,位錯(cuò)密度和點(diǎn)陣畸變明顯高于其他變形量熱軋后的.這種變化規(guī)律可以由動(dòng)態(tài)再結(jié)晶進(jìn)行解釋:在大變形熱軋過程中,晶粒通過在晶界等位錯(cuò)聚集處形核長(zhǎng)大發(fā)生再結(jié)晶 (非連續(xù)動(dòng)態(tài)再結(jié)晶),或由變形生成小角度晶界晶粒并在變形量進(jìn)一步增加時(shí)直接轉(zhuǎn)變?yōu)榇蠼嵌染Ы绨l(fā)生再結(jié)晶(連續(xù)動(dòng)態(tài)再結(jié)晶),隨后再結(jié)晶晶粒長(zhǎng)大,原始片層狀組織被逐步分解成超細(xì)晶[16].
由圖4 可見:經(jīng)變形量為 90% 的 大 變 形 熱 軋后,TC4鈦合金中含有大量因劇烈塑性變形而形成的 高密度位錯(cuò)、位錯(cuò)胞和亞晶等,其組織明顯細(xì)化;對(duì)選區(qū)電子衍射(SAED)花樣分析后發(fā)現(xiàn),衍射環(huán)由 密排六方和體心立方兩套斑點(diǎn)組成,分別對(duì)應(yīng)鈦合金的α和β相,衍射斑點(diǎn)呈不連續(xù)環(huán)狀,說明軋制后 TC4鈦合金組織中存在大量的大角度晶界[14,17];在 TEM 暗場(chǎng)像中可以明顯觀察到超細(xì)晶,統(tǒng)計(jì)得到的平均晶粒尺寸約150nm,由于此處使用 TEM暗場(chǎng)像測(cè)量的晶粒數(shù)量有限,所得平均晶粒尺寸與實(shí)際情況可能存在少許誤差.與大變形熱軋前的TC4鈦合金相比,經(jīng)90%變形量熱軋后合金的組織 明顯細(xì)化,采用大變形熱軋成功制備得到了超細(xì)晶 TC4鈦合金.
2.2 物相組成
由圖5可知:大變形熱軋前后 TC4鈦合金的組 織均由α和β相組成,熱軋前 TC4鈦合金中的β相 體積分?jǐn)?shù)約10%,其衍射峰強(qiáng)度較低,大變形熱軋 前后兩相的衍射峰強(qiáng)度變化不大,說明熱軋前后合 金中的α和β相含量基本保持不變;α(101 -1)面的衍 射峰在大變形熱軋后有明顯的寬化現(xiàn)象,說明軋制 后 TC4鈦合金的晶粒得到了細(xì)化,這與顯微組織的 觀察結(jié)果相符.通常 TC4鈦合金在軋制后會(huì)形成 (0002)織構(gòu),但由圖5可知只有當(dāng)變形量達(dá)到90% 時(shí),(0002)面的衍射峰強(qiáng)度才有適量提高,即(0002) 取向有所增大.這是因?yàn)殡m然動(dòng)態(tài)再結(jié)晶會(huì)消除形 變織構(gòu),但當(dāng)變形量達(dá)90%時(shí),形變織構(gòu)數(shù)量較多, 動(dòng)態(tài)再結(jié)晶會(huì)來不及完全消除形變織構(gòu)形熱軋前合金的874MPa提高了近30%,其伸長(zhǎng)率超過9%,呈現(xiàn)出高強(qiáng)高韌的特點(diǎn).
形熱軋前合金的874MPa提高了近30%,其伸長(zhǎng)率超過9%,呈現(xiàn)出高強(qiáng)高韌的特點(diǎn).
材料的強(qiáng)度與晶粒尺寸之間符合經(jīng)典的 HallGPetch關(guān)系,即:
式中:σy 為屈服強(qiáng)度;σ0 為材料常數(shù),與位錯(cuò)移動(dòng)時(shí)所受晶格阻力有關(guān);ky 為常數(shù);d 為平均晶粒尺寸.由式(1)并結(jié)合圖2~圖4分析可知:隨著熱軋變形量的增加,TC4鈦合金的晶粒尺寸減小,強(qiáng)度增加;經(jīng)90%變形量熱軋后 TC4鈦合金除了組織得到進(jìn)一步細(xì)化外,在晶粒內(nèi)部還出現(xiàn)了高密度位錯(cuò)、位錯(cuò)胞以及非平衡晶界,因此其強(qiáng)度增加顯著.此外,TC4鈦合金在強(qiáng)度提高的同時(shí)保持了優(yōu)異的塑性,這仍然要?dú)w因于組織的細(xì)化.在變形時(shí)位錯(cuò)可以在更多相對(duì)細(xì)小的晶粒中啟動(dòng),不同細(xì)小晶粒間的變形更容易協(xié)調(diào),從而推遲了應(yīng)力集中和斷裂的發(fā)生,提升了塑性.可見,通過道次大壓下量的大變形熱軋可以獲得高強(qiáng)高韌的超細(xì)晶 TC4鈦合金材料。
2.4 拉伸斷口形貌
由圖8可見,經(jīng)大變形熱軋后TC4鈦合金的拉伸斷口均呈韌窩狀,為典型的微孔聚集型韌性斷口.鈦合金受力時(shí),因位錯(cuò)的塞積作用,在晶界、亞晶界、析出相、夾雜物處首先形成微孔;隨著變形的繼續(xù),微孔相互連接并長(zhǎng)大,導(dǎo)致合金斷裂[18].隨著熱軋變形量的增加,韌窩尺寸減小、深度變淺,說明合金塑性變差.這是因?yàn)樽冃瘟吭酱?合金的晶粒尺寸越小,微孔形核數(shù)量越多。
3 結(jié) 論
(1)通過大變形熱軋及道次大壓下量的方法成功制備了超細(xì)晶 TC4鈦合金,經(jīng)變形量為90%的大變形熱軋后,可以獲得平均晶粒尺寸約 150nm的超細(xì)晶組織,合金的抗拉強(qiáng)度從874 MPa提升到1135MPa,伸長(zhǎng)率超過9%。
(2)TC4鈦合金在大變形熱軋過程中發(fā)生了動(dòng)態(tài)再結(jié)晶,隨著熱軋變形量的增加,超細(xì)晶數(shù)量增加、尺寸減小,晶粒內(nèi)殘留位錯(cuò)、亞晶等缺陷的密度增加,合金的硬度和強(qiáng)度增大;由于超細(xì)再結(jié)晶組織的形成,大變形熱軋后 TC4鈦合金仍然保持了優(yōu)異的塑性,拉伸斷裂方式均為韌性斷裂。
標(biāo)簽: